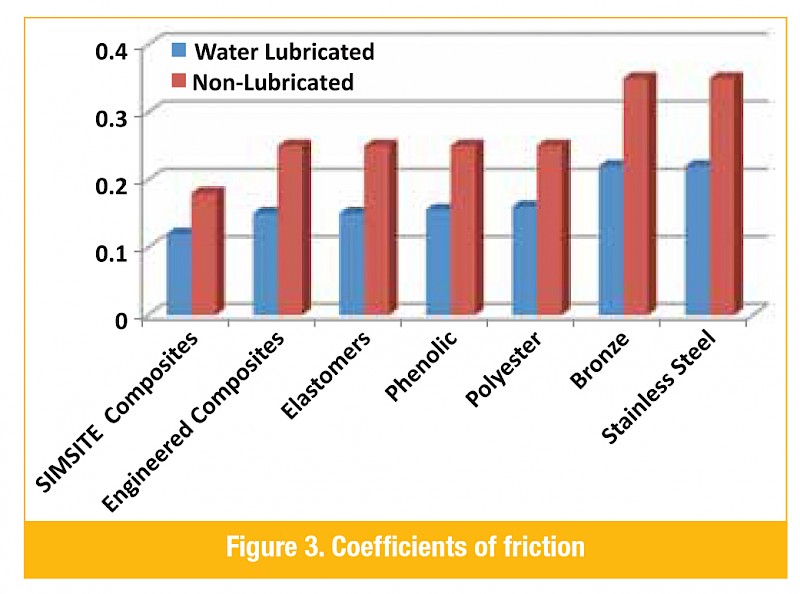
Structural Composite Parts
John Kozel, sims Pump company
Composites significantly reduce energy consumption, maintenance costs and repair costs.
Today, tremendous e ort is made to reduce energy con- sumption. e Department of Energy (DOE) and the Hydraulic Institute (HI) work together to reduce the energy consumption of pumps, motors and pump systems. is is where composites can be of great benefit they can significantly reduce energy consumption—in some cases by 20 percent or more.
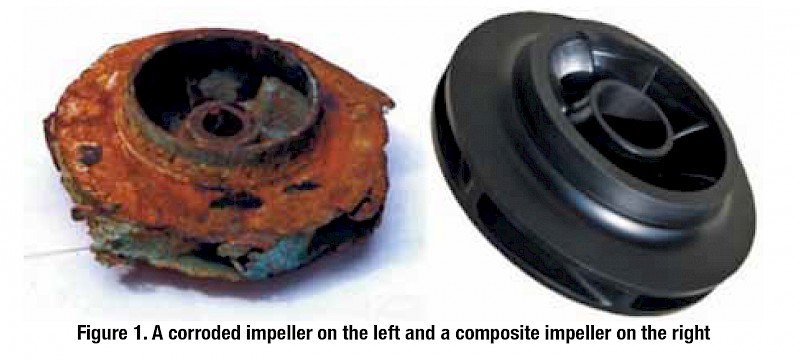
Corrosion, erosion, cavitation, rotor imbalance and leakage between the wear rings, casing rings and inter-stage bushings are major contributors to the loss of pump efficiency. Damage from corrosion, erosion, and cavitation quickly destroys the metallic pump and pump parts, which makes the pump inefficient and increases energy consumption.
As seen in Figure 2, energy costs dwarf any other expenses. Here, the acquisition cost is only 9 percent of the total life cycle cost of one pump.
is why the DOE, Europump, and the HI have focused on pump life cycle costs.
Composite Wear Components and Surface Finish
Wear between the rings and bushings create large clearances, which result in substantial decreases in pump efficiency as well as huge increases in the energy consumed to operate the pump.
Historically, most pump companies and repair facilities have used metallic parts for wear rings, casing rings, sleeves, bushings, and guide bearings. ese metallic parts have the potential to gall and seize and, therefore, require larger clearances between the parts. Compounding the issue is that these metallic parts do not have self-lubricating qualities as many composites do. Also, metallic parts are subject to corrosion, which further increases clearances and energy consumption.
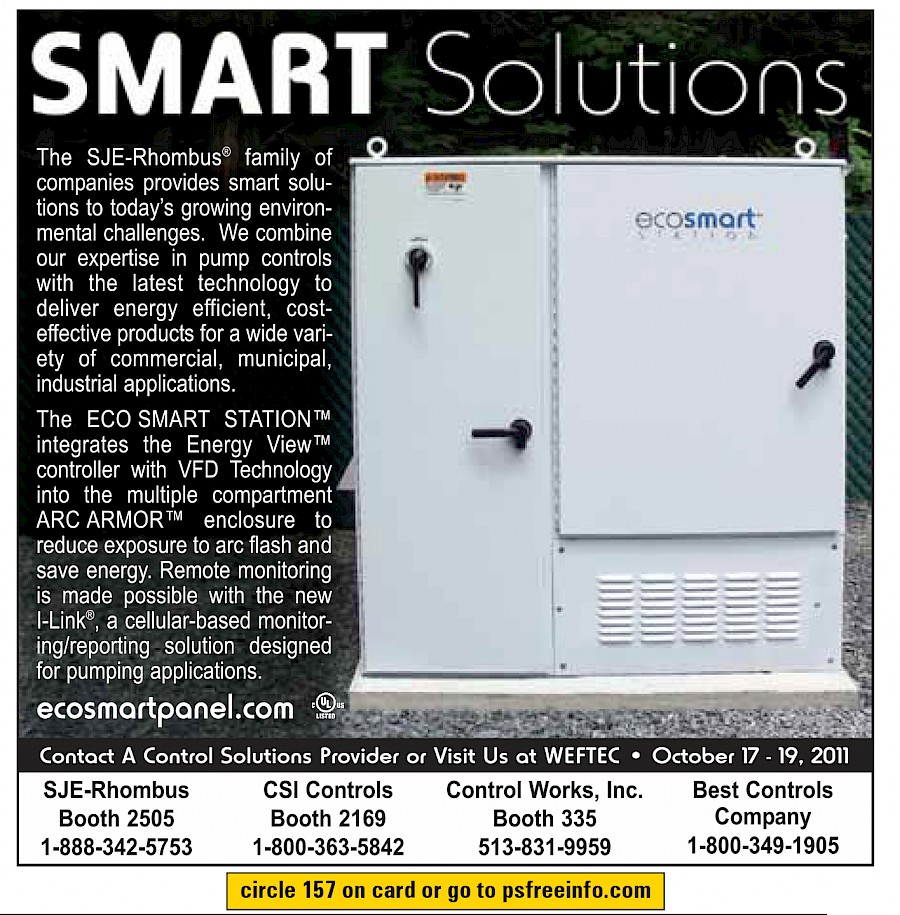
Thermoplastic and thermoset engineered composites have been used successfully to replace these metallic parts. In a structural composite the fibers are not chopped, cut or macerated. Thermoset structural composites have the mechanical strength of metal and have self-lubricating qualities embedded in the composite eliminating the risk for seizing and galling. Furthermore, these engineered composites have extremely smooth surfaces with an excellent surface finish and a low coefficient of friction on all surfaces. This low coefficient of friction increases efficiency and reduces
energy consumption. Because they will not seize or gall like metallic rings, they run with tighter clearances, which adds to the increased efficiency and decreased energy consumption.
Low Coefficient of Friction
As shown in Figure 3, most composites have a lower coefficient of friction than metallic materials—such as bronze or stainless steel—that have been traditionally used in pumps. Structural graphite composites and engineered composites have the lowest coefficient of friction, lubricated or non-lubricated. e low coefficient of friction reduces the friction losses of the liquid being pumped, which allows for an increase in efficiency and a reduction in energy consumption.
Composite coatings have been used to coat pump casings, which not only protects the casings against corrosion and erosion but also smooths the rough surfaces, reducing friction and increasing efficiency. Some studies have shown that e ciency can be improved by as much as 2 to 3 percent by using composite rings, guide bearings and coatings.
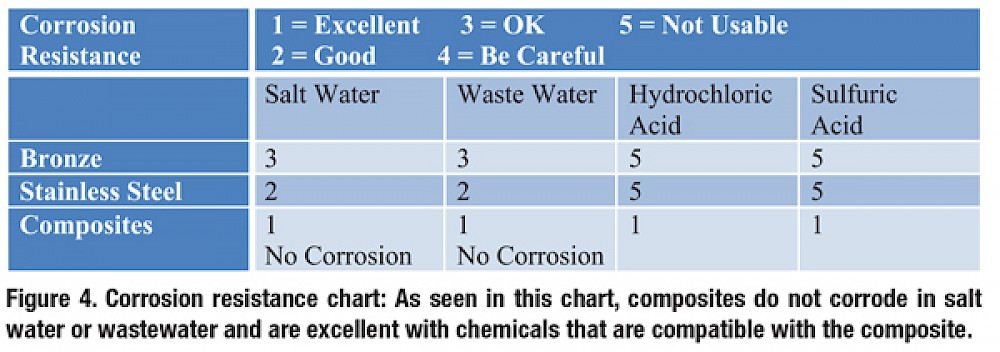
Since many composites are impervious to different corrosive environments, they will not corrode, or erode. Although composite wear components will reduce energy consumption for all pumps, including all fresh water services, the greatest savings occur in corrosive environments such as salt water, wastewater, chlorinated water and chemical processing because the composites, in many cases, will not corrode at all.
When metallic pump parts begin to wear from corrosion, pump efficiency drops drastically. The life cycle of the pump is often reduced to months instead of years.
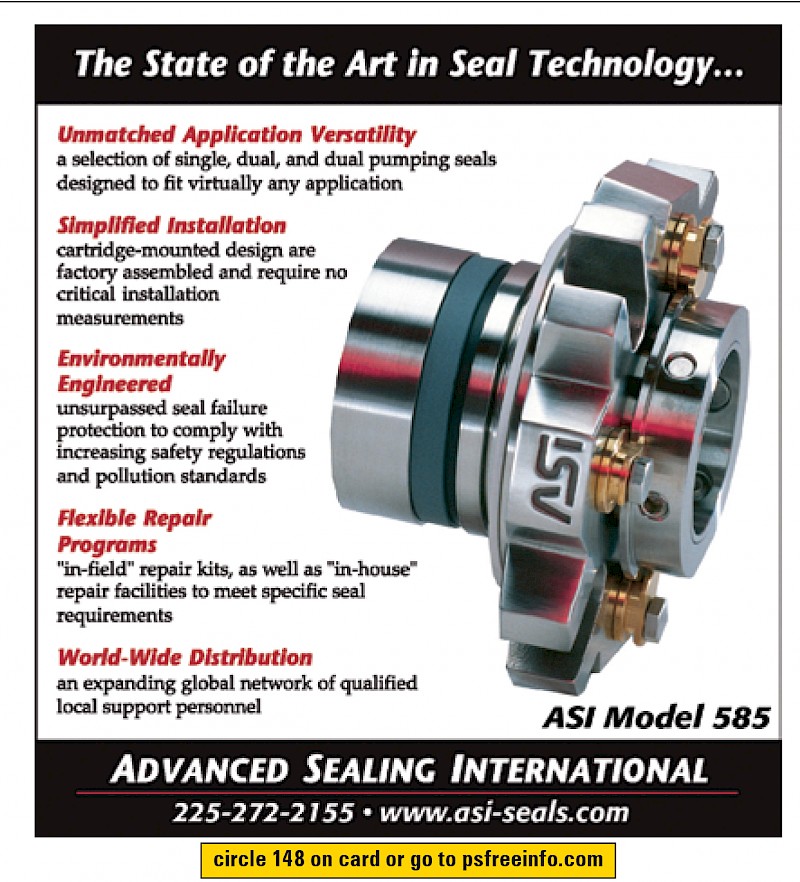
According to the DOE, many centrifugal pumps may be less than 50 percent efficient but have the potential to improve by 20 to 30 percent through upgrades and system changes. Pump upgrades can improve performance, maintenance and repair issues and improve efficiency, pump life and reliability. Pump upgrades prevent expensive products from deteriorating. They can prevent pump leaks that can result in costly cleanups and fines from regulatory agencies. In most cases, reduced down- time outweighs all other benefits.
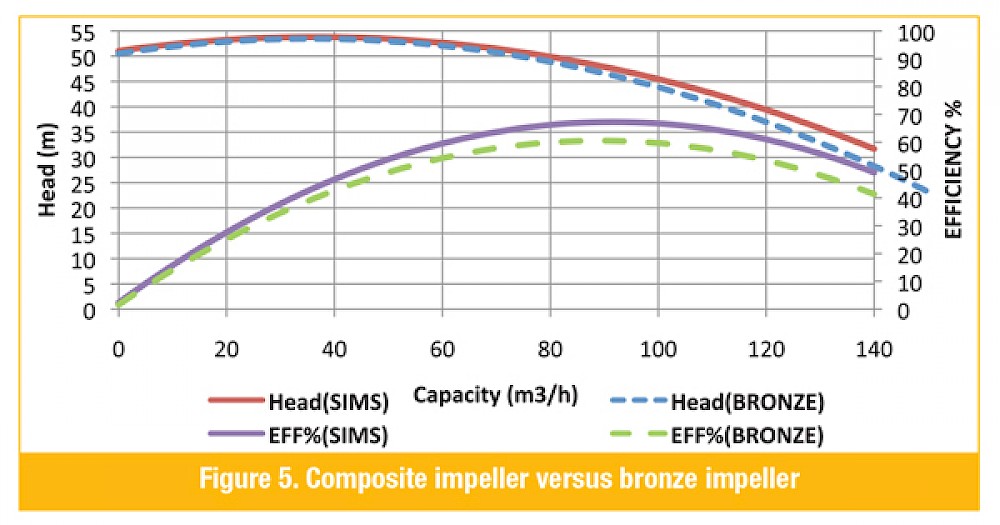
In difficult times, allocating the funds for the upgrades may be hard, but the payback is quick. The resulting savings frees up funds that otherwise would have been wasted on energy, and more expensive repairs at a later date. The incremental costs of upgrades are minimal when compared to the expense of downtime and repairs.
Plant outages, ship overhauls,
building new vessels, building new manufacturing plants, plant expansions and new system installations are
good opportunities to specify pumps
with upgraded efficiency and reliability features such as structural graphite
composite pump components (impellers, casing rings, sleeves, bushings, bearings and mechanical seals).
Lower Costs & Increased Performance
Because of the self-lubricating characteristics of many engineered composites and because composites do not wear or corrode, the performance curve will actually increase over time. A 1,000-hour performance test was made by Warren Pumps on a U.S. Navy standard fire pump manufactured from titanium used an engineered structural composite impeller and casing rings. The results clearly showed a substantial increase in the head-capacity (H-Q) Curve – 2.5 percent with the composite impeller and rings at the end of the 1,000-hour endurance test. The new alternative composite solutions for impellers and rings are excellent for new pumps, repairs or retrofit applications. They are lightweight and virtually indestructible. Wear of other pump parts, including the pump casing, is greatly reduced, because of the impeller’s perfect balance; lightweight; self-lubrication; sealing; and corrosion, erosion, and cavitation resistance.
Optimization
It is a common problem—a pump is purchased for one specific performance and when it is put into service, the pump operates at another point completely different from the original design point (best efficiency point BEP) because of the system requirements. When a pump is operated away from the BEP,
it causes problems, including excessive noise and vibration; shaft oscillation; cavitation; premature wear; and failure of the mechanical seals, bearings, rings, sleeves and impellers. In extreme cases, the pump shaft will break. These problems can be resolved by installing alternative solution impellers and rings which have been re-engineered for the system requirements.

The impeller is the heart of any centrifugal pump. Like a human heart, a pump impeller is the most loaded pump component, constantly stressed by hydrodynamic forces, fatigue, corrosion, erosion abrasion, chemical attack and cavitation. Engineered structural composite impellers offer potential to reduce energy consumption. Because of their corrosion, erosion and cavitation resistance, light weight, smooth vane passageway sur- faces, anti-galling and anti-seizing characteristics, composite impellers are able to operate at significantly higher efficiencies than metallic impellers. Composite impellers are machined as opposed to cast or molded which enables the composite impeller to be optimized hydraulically for the service in which the pump runs. Machining allows for perfect balance, both mechanically and hydraulically, because of the accuracy of the vane passages. These impellers may not go into imbalance even after years of service. This reduction in vibration translates into higher efficiency, a reduction in energy consumption and reduced maintenance.
The overall efficiency of a centrifugal pump is in direct correlation to the efficiency of the impeller. The impeller’s hydraulic design must correspond to the hydraulic design of the pump casing and to the operating conditions of the pump in service (in the plant) to maximize efficiency. Any centrifugal pump fitted with a structural composite impeller will save money for the pump owner and operator in repair and maintenance costs as well as in energy consumption.
Designed for Superior Hydraulic Performance
Because structural composite impellers are computer engineered, designed and precision machined, the impeller vane geometry can be engineered using CFD (computerized fluid dynamics) techniques and programs to maximize efficiency and performance. Problems such as recirculation, radial thrust and cavitation can be minimized or eliminated by using structural composite impellers instead of the traditional metallic ones. Impeller vane shapes can easily be modified to provide the best shape for the specific application and performance requests.
Composite Versus Bronze Impeller
Figure 5 shows that changing a bronze impeller to a structural composite impeller increased efficiency 15.8 percent. The efficiency on this 20 kilowatt pump (26.8 horsepower) went from 57 percent with a metallic impeller to 66 percent with a structural composite impeller—an increase of 9 points. At 0.11 cents per kilowatt hour this translates into a savings of $2,218.00 per year, per pump.
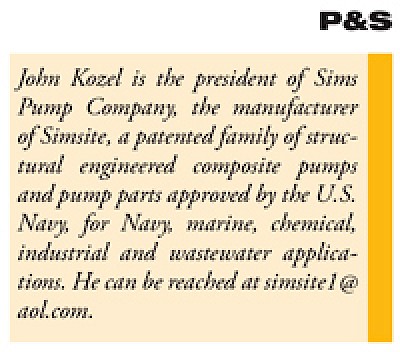
After only one year of service in a corrosive salt water environment, the bronze impeller began to corrode, further reducing efficiency. Depending on the service, the temperature of the salt water and how the pump was operating, the efficiency will be reduced by as much as 5 to 7 percent or more, resulting in additional energy costs.
Upgrading to a structural composite impeller will not only increase efficiency 15.5 percent from the start but will also prevent the losses in efficiency as a result of corrosion resulting in a total saving to the customer of more than 20 percent, which results in a savings of $4,155.00 per year per pump.